From Carbon to Algae: NetZero Strategies within Vale’s Clydach Nickel Refinery Decarbonisation
- Eric Lewis
- May 13, 2024
- 5 min read
Updated: May 15, 2024
In a world where sustainability is paramount, industries are increasingly seeking innovative pathways to reduce carbon emissions and embrace NetZero strategies. Among these pioneers is a distinguished nickel refinery, boasting over a century of excellence in producing high-quality nickel products. Established in 1902, this refinery stands as a cornerstone of the UK's industrial landscape, supplying class 1 nickel of unparalleled purity to over 280 customers across 30 countries.
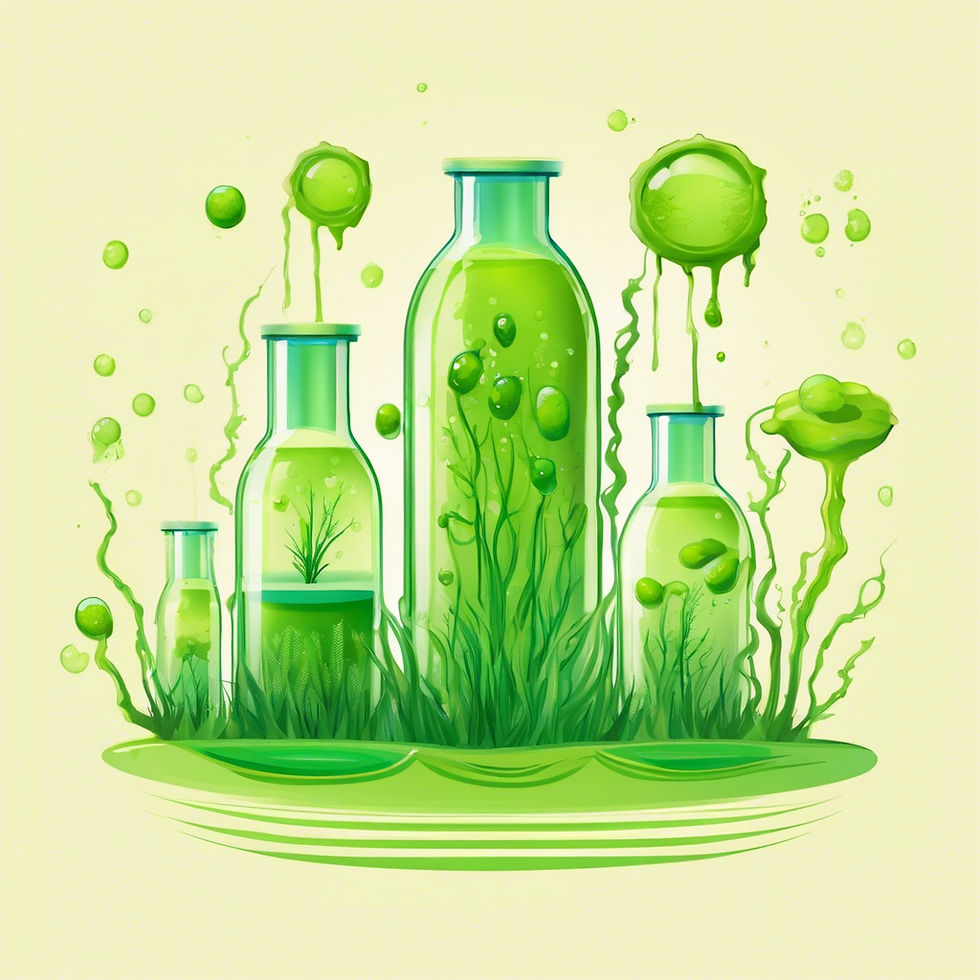
In our recent interview, we had the privilege of speaking with Peter Martin, the esteemed Technical Manager of Vale, the renowned company behind the innovative nickel refinery. Delving into discussions surrounding their decarbonisation pathways, Peter provided invaluable insights into Vale's strategic initiatives aimed at fostering sustainability within the industry. With Peter's expertise guiding the conversation, we gained a deeper understanding of Vale's proactive approach towards mitigating carbon emissions and charting a course towards a greener future for nickel refining.
“We started operation in 1902 as a nickel refinery and produce high quality (class 1 nickel at 99.9% purity) pellet and powders. We have a capacity of 40kT per annum and operate a 24/7 operation. We have 194 full time employees with a further 40 long term contractors on site. We supply nickel into over 30 countries and over 280 customers. We use the Mond Nickel Carbonyl process to purify a semi processed mixed nickel oxide feed (mixed with copper, cobalt, iron and trace PGMs). We are the only nickel refinery in the UK and one of only 3 or 4 in Europe. Nickel is primarily used in stainless steel but due to the quality of our nickel that is not the general use of our nickel. Our nickel will end up in coins, plating applications, powder metallurgy, catalysts, high purity alloys (aerospace and automotive) and batteries (both traditional batteries and now increasingly into electric vehicle batteries)”.
While traditionally synonymous with stainless steel production, the refinery's nickel finds diverse applications, from coins to plating, catalysts to batteries, including those powering the burgeoning electric vehicle market. Yet, amid its storied history lies a commitment to evolution, particularly in the realm of sustainability.
“Our process requires a large supply of hydrogen (approximately 2600m3/h) and carbon monoxide (approximately 350m3/h). Currently this is carried out in a Steam Methane Reformer which produces carbon diooxide on the combustion side and also the process gas side. We then also have natural gas used to heat one of our kilns and our pellet units (have 19 of these each with their own furnace). All this equipment was built in the 60’s-70’s so although the burner management systems have been updated the physical equipment is out dated. The large number of pellet units means a large number of smaller flues to try to capture the CO2 from. We also have a base load of around 4MW of electricity usage on site. We also have a fairly large site (53 acres) with the main plants spread across this space meaning we do not only have a high number of CO2 discharge points but also, they are dispersed around the site making capturing the CO2 and getting it to a central storage location is not straight forward. The other challenge is how to produce our hydrogen and carbon monoxide in a low carbon way that is also cost effective”.
The refinery's journey towards decarbonisation is multifaceted, rooted in a comprehensive understanding of its processes and challenges. From the need to reduce reliance on carbon-intensive hydrogen and carbon monoxide to the imperative of modernizing aging infrastructure, the path to sustainability is rife with complexity. However, through strategic foresight and collaborative efforts, the refinery is forging ahead, exploring diverse decarbonisation pathways with unwavering determination.
“We have been looking at different methods to generate our hydrogen and carbon monoxide in a low carbon way. For this we have looked at ‘blue’ hydrogen options as well as some ‘green’ hydrogen ones (like electrolysis). We have also then looked at producing enough hydrogen by these methods so we can they replace the natural gas we use a fuel on site with hydrogen. We have also looked at self-generation of electricity on site via a CHP system with pre combustion carbon capture built into the design. We are also exploring the use of solar energy on site and looking to install 500kW of solar on a roof of one of our buildings.
Due to there being no local geological storage sites for CO2 in South Wales a storage option for any CO2 we capture would be expensive due to the shipping required. Hence, we have always felt a usage option would be better for us and if we could find one that was financially viable then even better. Through work we were doing with SWIC (South Wales Industrial Cluster) we were introduced to the work the RICE (Reduction in Industrial Carbon Emissions) group in Swansea University were doing around algae. This allowed us to work in collaboration with them to demonstrate that algae could be grown from industrial CO2 and that high value products could then be extracted from this. This first demonstration plant used natural light but has led us to now be working with Swansea University and a company (Remediiate) on a new design of internally lit reactor. This uses LED lights in the reactors so that the algae can absorb CO2 day/night and winter/summer at a constant rate. This new demonstration plant is currently under construction at site. Also, as part of this work we are carrying out early engineering studies to understand how we could leverage this technology to be able to absorb all the CO2 we currently generate on site”.
One such pioneering initiative involves the conversion of captured carbon into algae, a venture propelled by collaboration with academic and industrial partners. Through ground breaking research and development, the refinery aims not only to mitigate carbon emissions but also to harness algae's multifaceted potential, from vegan proteins to high-value pigments, with the ultimate goal of achieving a fully commercial solution capable of absorbing all on-site CO2 emissions.
“Algae is rich in proteins, lipids and pigments. One of the algae strains we have grown, spirulina, is used as a vegan protein and can be found in various forms in health food shops and supermarkets. Some of the pigments have a very high value with one of them worth up to £350/mg. Algae can absorb up to 2 tonnes of CO2 for every 1 tonne of algae grown making them a very efficient at absorbing CO2. Other uses of algae can be into animal feed and there has been a study that shows feeding algae to cows reduces the methane produced by the cows. It can also be used as fish food and can be used to displace Brazilian soy in salmon farms in the UK (the added benefit is that the algae will contain the pigments to give the salmon their natural pink colour without the need for artificial colours that are needed if feeding them soy-
based foods). The first demonstration plant showed that industrial CO2 could be used to successfully grow algae and that these high value pigments can also be harvested and purified. This first farm is currently being taken over in by a commercial enterprise to take it from the demonstration plant into a fully commercial one. The second farm is hoped to demonstrate how we can develop this to a scale that is able to take all the CO2 from the site, but it will be 2+ years before we are able to show this”.
The journey from carbon to algae within the nickel refining industry unveils not just a narrative of innovation, but a testament to the resilience and adaptability of industrial practices in the face of environmental challenges. The endeavours of this pioneering refinery underscore a commitment not merely to meet regulatory requirements, but to embrace a proactive stance towards sustainability, driven by a vision of a cleaner, greener future.